Med internationellt ledande teknologi vill vi skapa tillväxt på hemmaplan.
Bretzel GmbH uses Yaskawa drive technology
- Branscher
- Metallbearbetning
- Kund
- Bretzel GmbH
Challenge
CNC milling with the highest precision and dynamism
Bretzel GmbH Antriebs- und Elektrotechnik opted for YASKAWA’s EtherCAT-capable Sigma-5 servo drive system for the customized equipment of CNC milling machines. The drive solution guarantees the highest standards in terms of dynamics, precision and performance.
The company, located in Eschborn/Germany, delivered a large part of the required automation components to a CNC manufacturer supplying customers in the tool- and mold-making industry. Joint solutions for existing and new CNC machines are developed in close cooperation with the control manufacturer. A PC-based, high-performance CNC kernel is used here. The NC kernel and downstream CoDeSys PLC run independently of the other processes in the PC in real-time operation, enabling jerk-free movements even in complex geometries.
Up to nine synchronous axes are currently supported in interpolated traversing. Fig. 1 shows a small 4-axis machine in whose X-axis two parallel servo axes were incorporated in the so-called gantry operation. Regardless of NC-capability, a complete Windows interface is automatically available to the machine, offering users all modern network and connection options.
Powerful drive technology
The axes of the CNC machines are driven by Yaskawa Sigma-5 servo motors. More specifically, Bretzel opted for models of the SGMAV series. The Sigma-5 servo system is a servo drive consisting of servo motors, servo amplifiers and powerful Sigma Win+ setup software (Fig. 2). The series comprises rotatory motors, direct drives and linear motors. With short positioning times, the standard models achieve a high positioning accuracy of more than 1 μm.
As a highly dynamic servo system, the Sigma-5 provides for minimum milling times. In addition, the motors are characterized by extremely precise and practically wear-free running. An absolute 20-bit encoder system with over 1 million increments per motor revolution detects the precise position of the motor at any time. The compact dimensions and low-inertia configuration permit enormous acceleration.
Thanks to a so-called auto-tuning function for automatic drive optimization and an automatic filter function to suppress vibration, Sigma-5 motors also run quietly and virtually vibration-free at low speeds. Optimum operation is thus guaranteed in high-precision applications. At the same time, machine wear is reduced, with a positive effect on life-cycle costs.
Commissioning and diagnosis of Sigma-5 components are simple and fast with the userfriendly SigmaWin+ software. Manual settings or special expertise is unnecessary. The autotuning algorithm permits the perfect set-up of, for example, two axes in high-performance machines in less than two hours – instead of the usual eight.
Solution
EtherCAT real-time bus system
Modular interfaces to EtherCAT, CANopen, POWERLINK and MECHATROLINK-II and III exist for the integration of Sigma-5 servomotors in extensive automation solutions. The Bretzel solution combines the Sigma-5 servo system with an EtherCAT interface. Servo controllers of the SGDV series with the EtherCAT option card make this possible. The servo controllers are supplied with 1 x 230V. Load and logic voltage are separately connected. The controllers offer an approved safe stop which enables them to reliably shut down in the case of an emergency stop despite the applied load voltage.
This fast EtherCAT real-time bus system ensures maximum performance while providing full access to all control registers and status information. In addition, the NC control permits the performance of multi-axis synchronous interpolated path movements.
Communication ensures via the cross-manufacturer standardized protocol CANopen (CoE = CANopen over EtherCAT). The EtherCAT CoE interface enables the construction of synchronized, distributed drive systems with a higher data transmission rate and greater reliability. 3-dimensional milling motions can thus be executed with the highest degree of contour accuracy.
V1000 compact AC drive
In addition to the Sigma-5, a further Yaskawa component was employed in the CNC milling machines configured by Bretzel: the spindles are controlled by a compact V1000 vector inverter, Fig. 3). Where permanent magnet motors can be precisely and reliably controlled, this frequency inverter provides a reliable and efficient solution. With its highly dynamic current vector control (open loop vector) it optimally drives both asynchronous and permanent magnet synchronous motors in the power range 100W to 15 kW. Even at extremely low speeds at least a nominal torque is achieved. As a standard, the V1000 can supply up to 400 Hz on the output side. In the case of a 2-pole spindle this is equivalent to synchronous 24,000 revolutions per minute. A software version with up to 1,000 Hz exists for faster-rotating spindles. Introduced as the world’s smallest compact frequency inverter, the V1000 has the advantage of requiring very little space.
Result
Yaskawa Sigma-5 servo drive system and V1000 compact AC drive have enabled Bretzel GmbH Antriebs- und Elektrotechnik to customize the equipment of CNC machines. The result is a particularly high degree of dynamism, precision and performance.
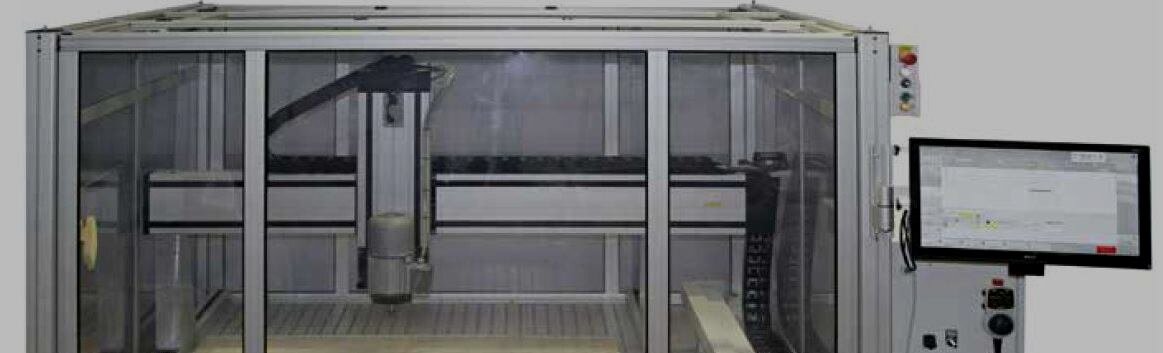